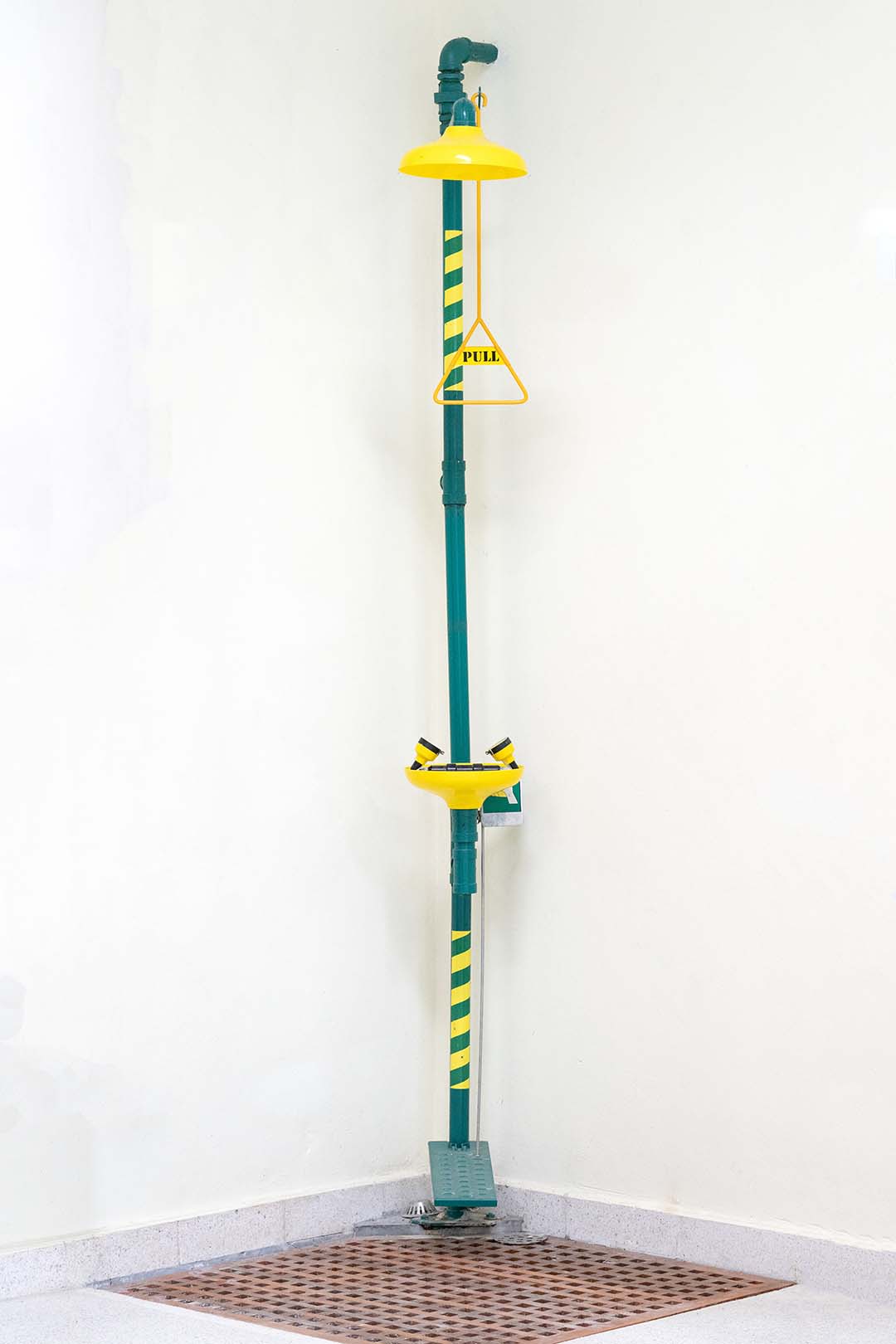
How Eyewash and Emergency Showers Help Prevent Long-Term Worker Injuries
The Occupational Safety and Health Administration (OSHA) requires eyewashes and emergency showers for workers who could be exposed to corrosive chemicals in the workplace. Workers use eyewashes, face washes and showers to flush chemicals and debris out of their eyes and off their bodies. If your facility requires an eyewash or emergency shower, you should know how they work, where they need to be located and how to use and maintain them.
OSHA and ANSI Requirements
OSHA requires eye/face washes and showers when working with or around corrosive chemicals, or equipment that can contain corrosive chemicals, such as:
- Anhydrous ammonia
- Formaldehyde
- Open surface tanks
- Forklifts and other powered industrial trucks
- Telecommunications batteries
- Paper and pulp-making equipment
OSHA does not have a specific standard or requirements for how eyewashes and showers are designed and installed. Instead, OSHA defers to the American National Standards Institute (ANSI) for these specifications. ANSI Z358.1 provides guidance for eyewashes and showers in situations where employees are exposed to “hazardous materials” such as caustic chemicals and other materials that can negatively affect human health. ANSI’s standard also provides functionality guidelines for eyewashes and showers, including flow rate, temperature and corrosion resistance.
Types of Eyewashes and Showers
There are two primary types of eye/face washes and showers: plumbed stations and self-contained stations. Plumbed stations are permanently connected to a potable water source, usually the same water source as your facility’s sinks. Self-contained stations are stand-alone devices with bottles of water or flushing fluid that need to be refilled or replaced after use. All eyewashes and showers must deliver water or tepid flushing fluid between 60 and 100 degrees Fahrenheit (15.5 – 37.7 Celsius) for at least 15 minutes.
Eyewash and Shower Locations
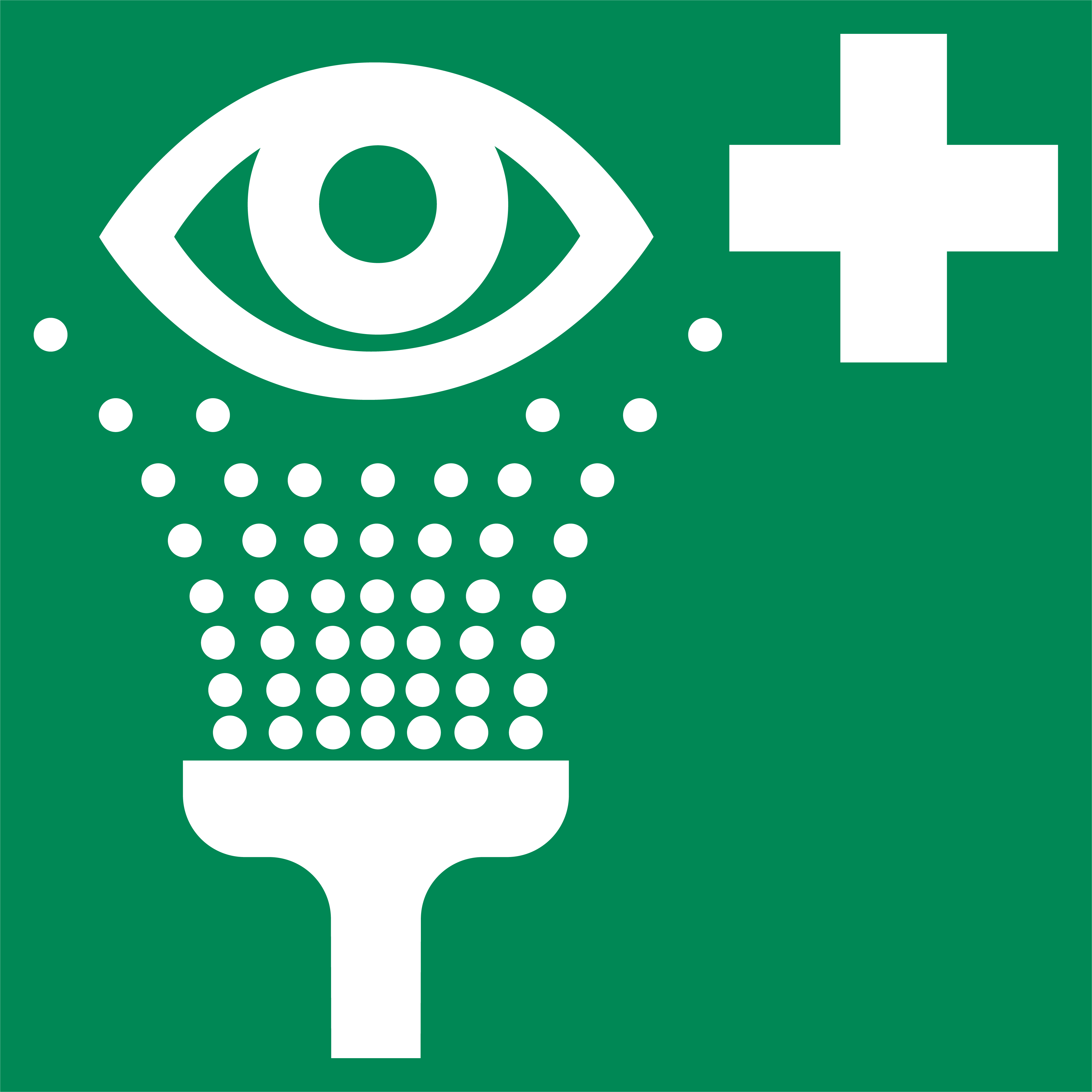
Both showers and eyewashes must be installed in areas where workers can reach them within 10 seconds. Work areas with harsher corrosive chemicals may need closer showers or eyewashes. Eyewashes and showers should be installed in well-lit locations with signage and must be on the same level as the work area’s hazards. Eyewashes and showers must keep water or flushing fluids between 60 and 100 degrees Fahrenheit, even if they’re installed outdoors or in cold or hot indoor environments. Keep paths and walkways clear so eyewashes and showers can be accessed in an emergency. Do not store materials in front of eyewashes or showers and clean up any debris or obstructions that could block them. Workers should be trained on where the closest eyewash and shower stations are to their work areas and on how to activate them.
Eyewash and Shower Inspections
Eyewashes and showers are vital pieces of emergency equipment that need regular maintenance and inspection to keep workers safe. Plumbed showers and eyewash stations should be turned on for a few minutes at least once a week to ensure they still work, and to flush out bacteria, sediment, or any other blockage in the plumbing. Self-contained or gravity-fed showers and eyewashes should be visually checked weekly to make sure that their flushing fluids haven’t run out or passed the expiration date on the container. Empty or expired bottles of flushing fluid must be replaced immediately. Finally, employers should ensure that all showers and eyewashes receive a full annual inspection to make sure they still meet ANSI guidelines.
Eye and Face Wash Specifications
- Eye and face wash valves must open within one second of the user turning on the wash station.
- Valves must stay open on their own until the user turns off the wash station.
- Many eyewash stations also include face washing attachments. These will either have large spray heads that can rinse both the eyes and face, or a special face-spraying ring in addition to the eyewash spray heads.
- Eye and face wash heads must be installed at least 6 inches from the nearest wall or other obstruction.
- All valve heads and flushing units must be protected from dust, chemicals, bacteria and other contaminants.
- Users must be able to remove protective devices from valve heads and flushing units with the same motion that turns on the wash station.
Emergency Shower Specifications
- An emergency shower must start within one second of the user activating it.
- Shower heads must be positioned between 82 and 96 inches above the work surface.
- The center of the shower head’s spray pattern must be at least 16 inches from the nearest obstruction.
- Showers must be capable of delivering 20 gallons of water or flushing fluid per minute.
Using Eye and Face Washes
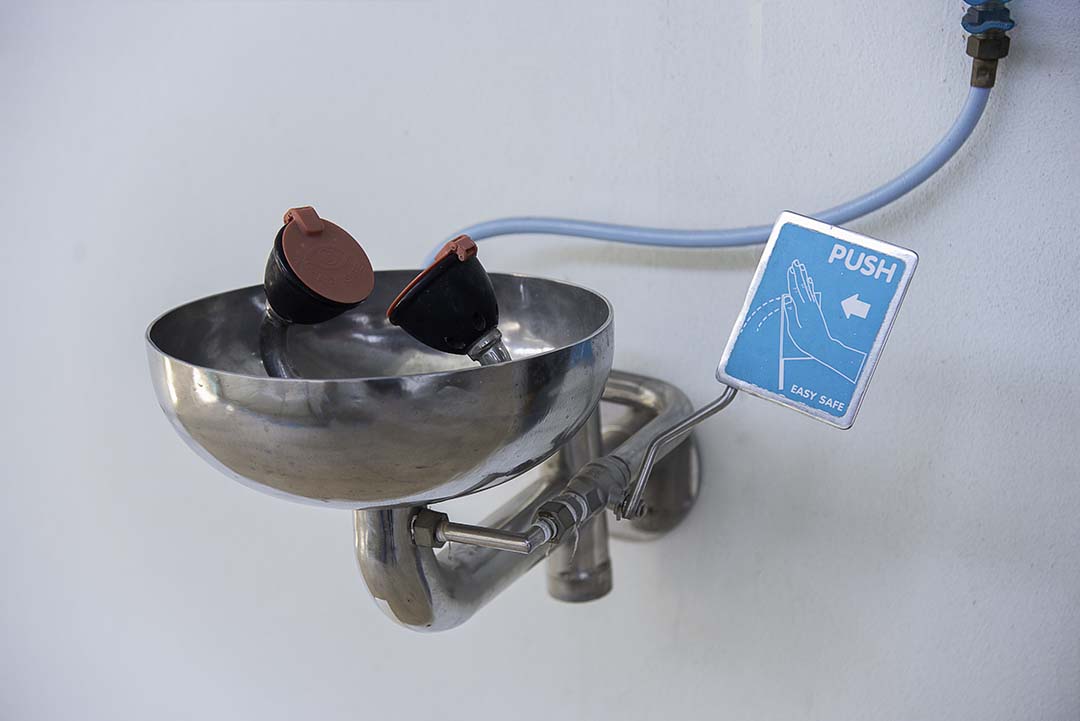
It’s important to train employees on how to use the eyewash and shower equipment in their work areas. Specific equipment design will vary and holding your eyes open under running water can be difficult, so employees should practice using their eyewash before they begin work. When using the eye or face wash, employees should activate the station, hold their eyes open, and roll them around to rinse the entirety of each eye. Contacts should be removed as soon as possible to keep chemicals or debris from getting stuck behind the lenses. Continue rinsing the eyes for at least 15-20 minutes, unless the chemical’s safety data sheet (SDS) recommends a longer rinse. Exposed employees should continue following the SDS’s first aid measures and seek medical attention right away to avoid long-term damage.
Using Emergency Showers
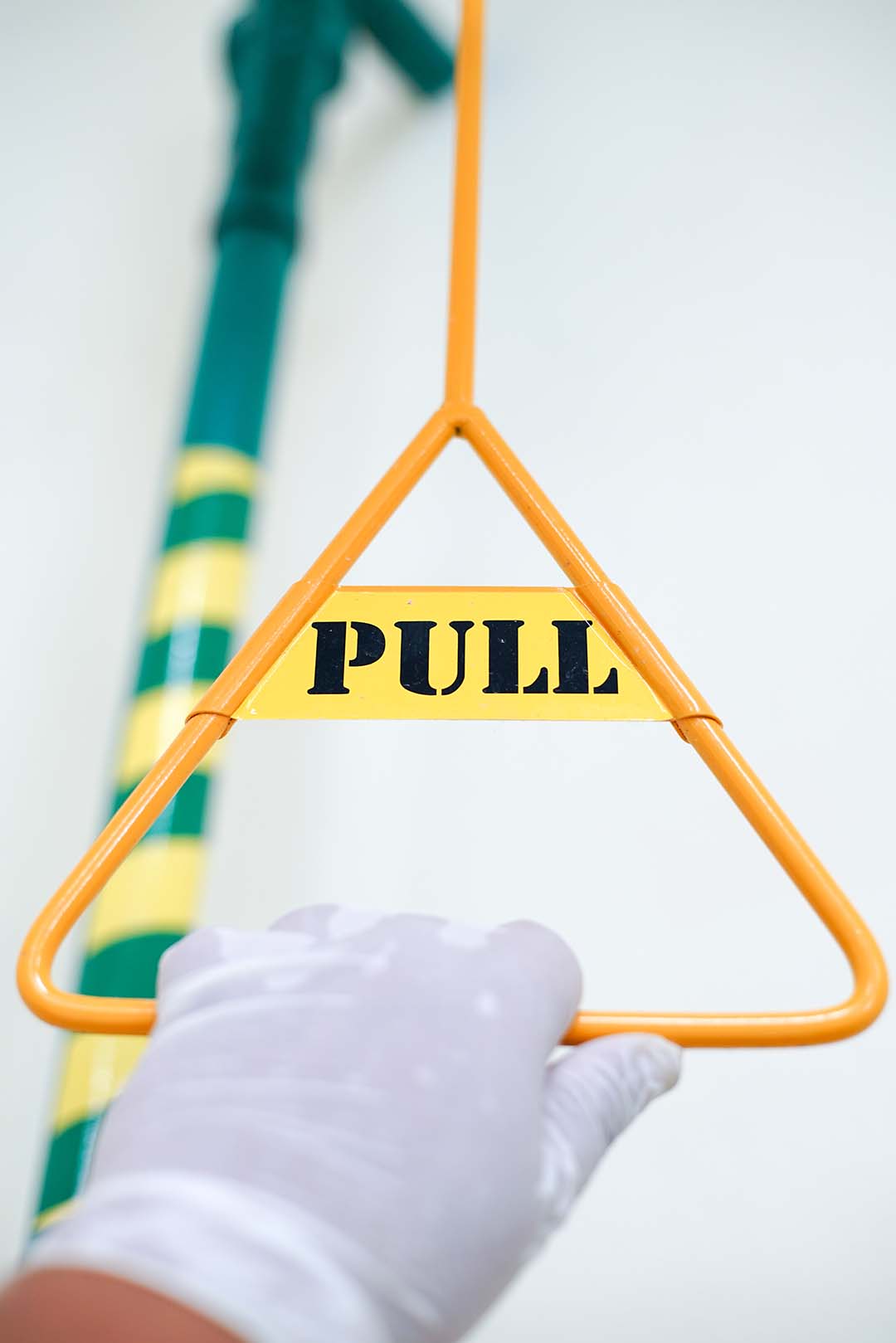
Emergency showers are operated similarly to eyewash stations, but employees should still be trained on their use. An employee that is splashed with a chemical or hazardous material should immediately head to the shower and start flushing water over affected body parts. They should also remove any items splashed by the chemical, such as contaminated clothing, shoes, or personal protective equipment, and keep rinsing all affected body parts for at least 15 minutes, unless the chemical’s SDS recommends a longer rinse. Employees should continue following the SDS’s first aid measures to avoid long-term injuries and seek medical attention if the SDS calls for it, or if they still feel burning or other symptoms.
Conclusion
Any employee who works around corrosive or caustic chemicals could be injured by those chemicals. Employees need to be able to react quickly and have access to eyewashes or showers to keep chemical splashes from turning into severe, life-altering injuries.
For more information on ANSI and OSHA requirements for eyewash equipment, check out this OSHA Letter of Interpretation about eyewash equipment. SafetySkills also offers awareness training over eyewash and emergency shower specifications and usage.
Discover more SafetySkills courses today!
TRY SAFETYSKILLS FREE FOR 14 DAYS
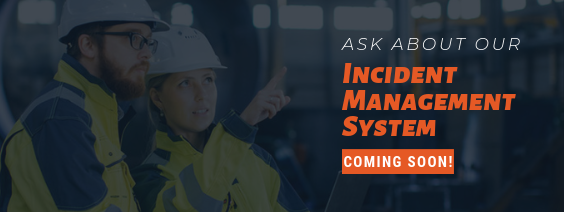